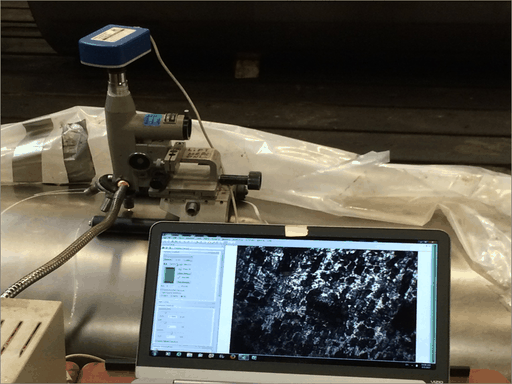
It is well understood that material processing directly influences microstructure and, consequently, the resulting thermo-physical and mechanical properties. The stability and nature of that microstructure ultimately govern how a material performs under service conditions.
In an ideal scenario, customers define clear specifications (SPECs), and manufacturers follow their established standard operating procedures (SOPs) to meet those requirements. This process works smoothly for well-established, commercially available materials and known applications.
But what happens when there is a subtle shift in service conditions or application environments, so that one is not fully recognized by either party?
What if that change leads to reduced service life or even premature failure? Suddenly, the manufacturer is faced with a performance claim.
At that point, a critical question emerges:
Was the failure caused by inherent material imperfections, insufficient properties, or unexpected service-induced loading?
No one wants to engage in finger-pointing. But unfortunately, disputes often arise: straining relationships between customers, suppliers, and producers. When failures repeat in the field, each side begins building its case, bringing in independent labs, consultants, and experts to validate their position. The result? Escalating costs in time, money, and trust.
At the core of Redtech Alloys team is the field-proven approach and understanding of the foundational “Processing – Microstructure – Properties” triangle, framed within the context of Product Lifecycle Management (design – mixing chemistries – production – usage – performance data analysis).
We take into account how the microstructure evolves during manufacturing and responses to the service conditions as a function of the part size and configuration. This includes scaling effects and localized variations, e.g., naturally occurring micro- and macro- chemical segregations. The “fly-through” microstructure clip shows an example of the composite microstructure at bulk- and nano- level resolutions, “invisible” factors that often go overlooked, but can critically influence long-term performance, hence, business and economics.
By combining advanced modeling with field testing and laboratory characterization, we enable accurate prediction and validation of microstructural distribution across real components. This allows refinement of specifications (SPECs) to better reflect the realities of evolving service conditions, rather than relying solely on legacy standards.
Our mission goes beyond preventing catastrophic failure. We focus on unlocking the full potential of commercially available materials by improving and optimizing them for performance, durability, and cost-efficiency, and all without requiring capital investment in new equipment. By tailoring and fine-tuning existing OEM processing parameters, clients often see measurable gains in energy savings, throughput, and overall product reliability.
This is why you can NOT afford to let the MICRO-world bring you MACRO problems!